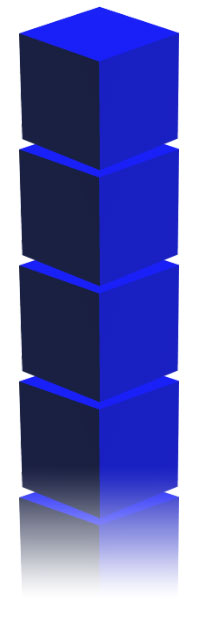  |
 |
 |
 |
Aluminum 6013
|
 |
Casting
|
 |
|
 |
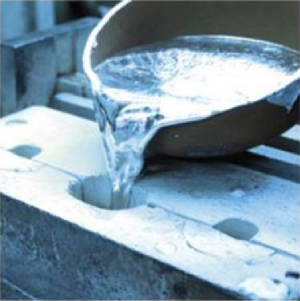
There are several different methods used to cast a wide range of parts in industry. These methods vary in there technique
and machinery but all serve the same basic purpose of creating a solid object usually multiple times. When determining the
casting process that is most practical for an application, several factors should be taken into consideration. One of the
most important of these considerations concerns the material to be used. In general, Aluminum is an excellent material to
cast with. It is one of the few materials that can be used in all casting methods.
For Aluminum 6013, die and sheet forming are often used to create parts. Aluminum alloys, such as Al 6013, are more often
used than pure aluminum for several reasons. First of all, pure aluminum is very hard to obtain and sustain due to its tendency
to openly oxidize with air. Secondly, the aluminum alloys have properties much more suitable for structural and other engineering
applications.
|
|
As aluminum 6013 can be used in all methods of casting the shape, size, cost and relative complexity of the part should be
used to determine the appropriate casting method.
For smaller parts either a form of die casting or investment casting can be used. Investment casting, with its higher
capital costs but lower per part costs, would be used for more complex parts whereas die casting would be used for less complex
parts. Some examples of parts that can be made using these methods are seats and seat components, housings, brackets and
pipes.
For larger parts, sand and continuous casting could be used. These forms of casting are less precise and are used to
make more general shapes that will be joined or reworked afterwards. Some examples of parts that can be made using these
methods are inner wall and floor panels for transportation vehicles and exterior body panels.
|
|
|