Method
We took measurements of the
width, thickness and length of the gauges (central area of the machined, dog bone-shaped samples) before performing the tensile
test on the three Al6013 samples (casted, welded and heat-treated). To continue, we calibrated the Instron machine and located
the samples securely into it. Then we run the test: a static load was applied until fracture. Force and elongation were recorded
throughout the test.
We used
the collected data to plot strain vs. stress curves for each of the three scenarios (casted, welded, heat-treated) and, based
on these plots, we determined the mechanical properties of each sample. Finally, we compared the samples based on their properties
to determine whether casting, welding and annealing affect the Al6013 samples in a desirable way, i.e. whether these processes
enhance the properties that make this alloy appropriate for the manufacture of fuselage panels.
Results
· Initial dimensions
of the tensile tested samples
Al6013 Sample |
Length
in m |
Width
in m |
Thickness
in m |
X-sectional
area in m |
Casted |
0.081407
|
0.0133096
|
0.0033528
|
4.46244E-05
|
Heat-treated |
0.0799084
|
0.0130302
|
0.0034544
|
4.50115E-05
|
Welded |
0.080518
|
0.0130048
|
0.0033528
|
4.36025E-05
|
· Strain vs.
Stress plots
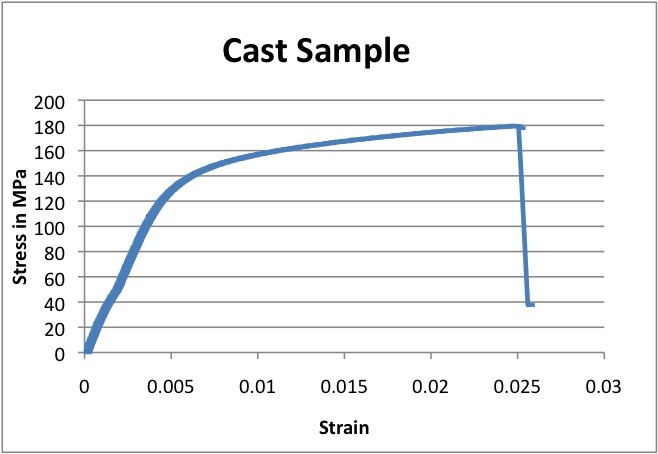
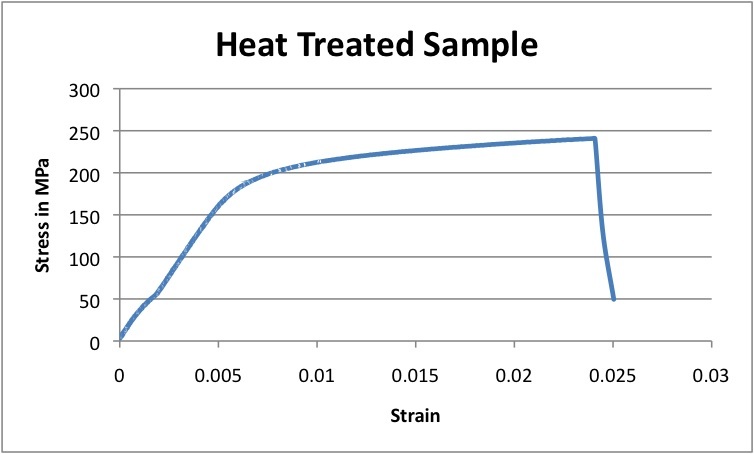
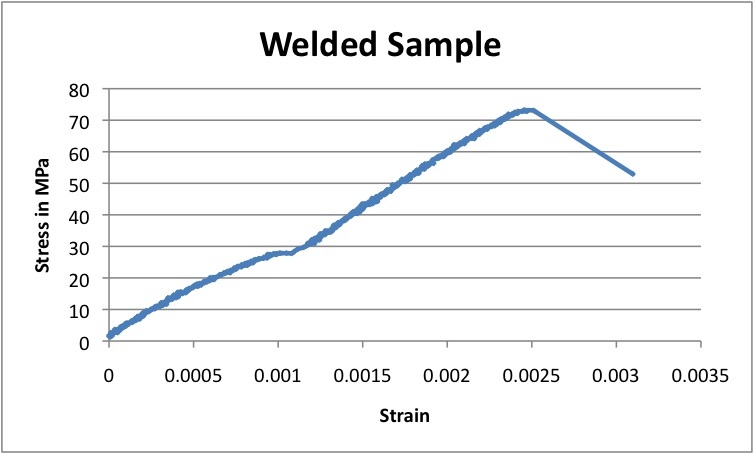
Analysis
·
Mechanical properties
of each sample
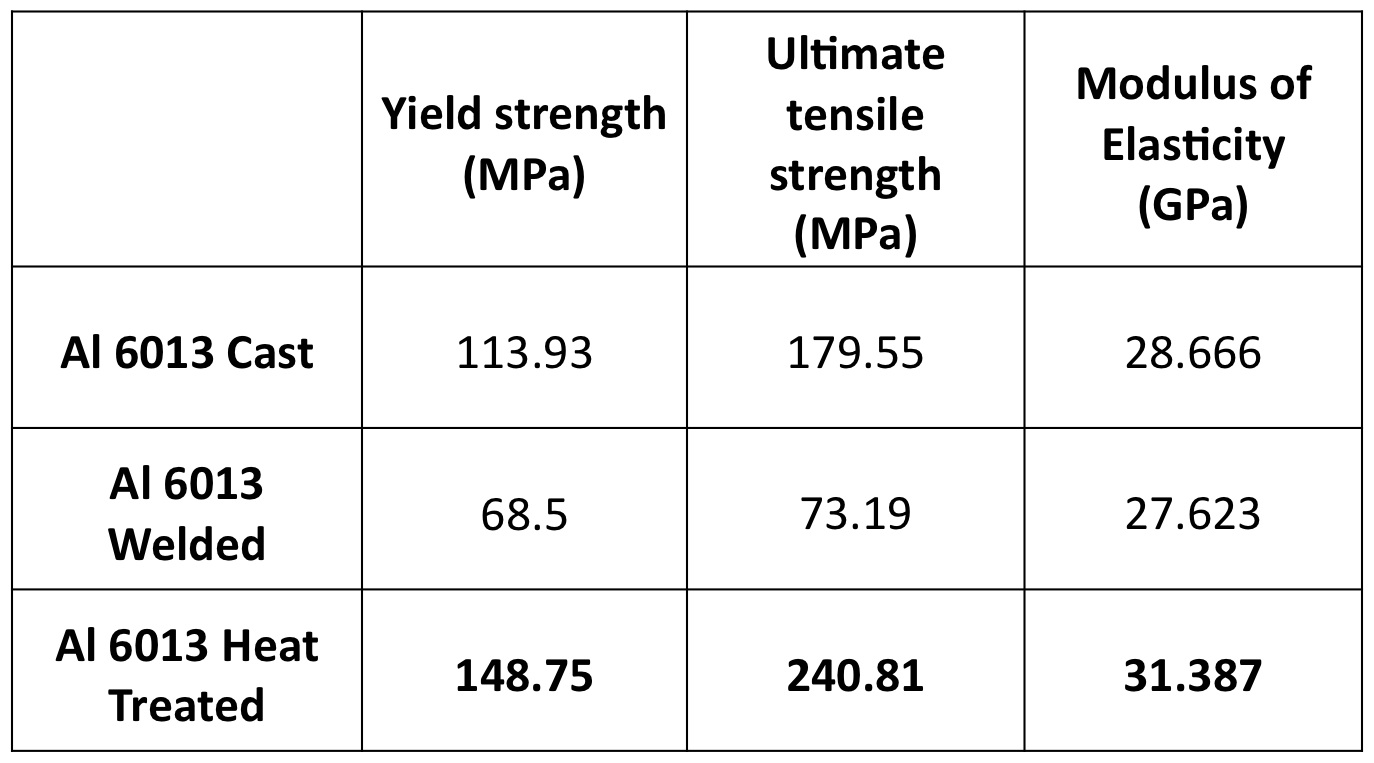
o The
yield strength for each case was determined graphically, the last point in the
elastic deformation area.
o Ultimate
tensile strength was also determined graphically: the point in the plot
corresponding to the highest stress experienced.
o To
find modulus of elasticity, we fitted a trend line to the elastic deformation
regions. The slope of such lines is the modulus of elasticity.
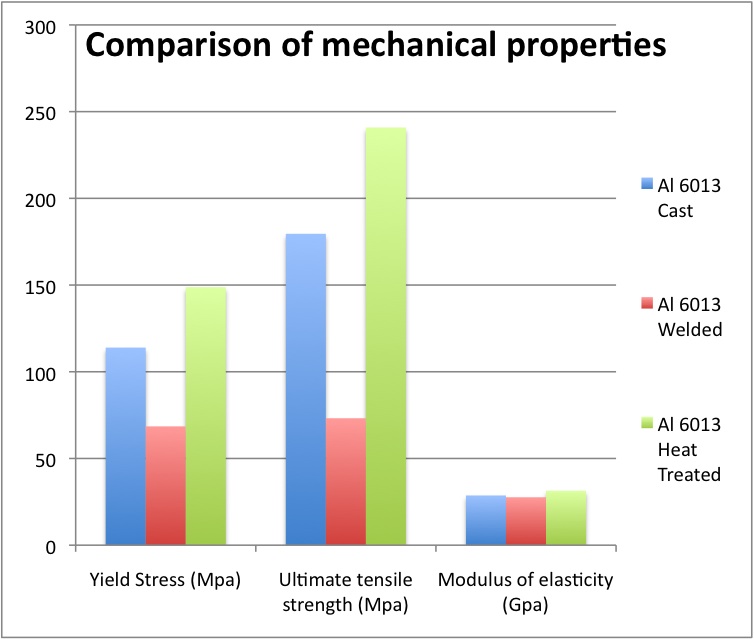
As illustrated
by the graph above,
the heat-treated sample was stronger both in terms of yield strength and
ultimate tensile strength. This is explained by the different microstructure of
this sample, produced by the heat treatments. Higher strength results from the
smaller grains created during heat-treatment. Given that there are more grain
boundaries in the microstructure after the hardening processes, dislocations
movement is more limited which is analogous to higher strength.
The
significantly lower strength of the welded sample (both in terms of yield
strength and ultimate tensile strength) can be attributed to the welding
process. Due to the material loss that results from welding, the sample’s gauge
was thinner than the other samples (especially at the weld.) This explains why
the sample fractured exactly at the weld.
Additionally,
and as illustrated by the strain vs. stress plots, the welded sample underwent
very little (almost none) plastic deformation. Welding makes Al6013 brittle,
which is responsible for the absence of plastic deformation. For the
manufacture of fuselage panels, brittleness is highly undesirable due to the
higher danger imposed by panels that will immediately fail, instead of first
deforming, then subjected to too high levels of stress.
Given
that strength is a desirable property for the manufacture of fuselage panels,
we concluded that heat-treating had a positive effect on Al6013 and welding had
a negative effect on it. Hence, Al6013 should be heat treated but not welded
prior to the actual manufacture of fuselage panels.
|